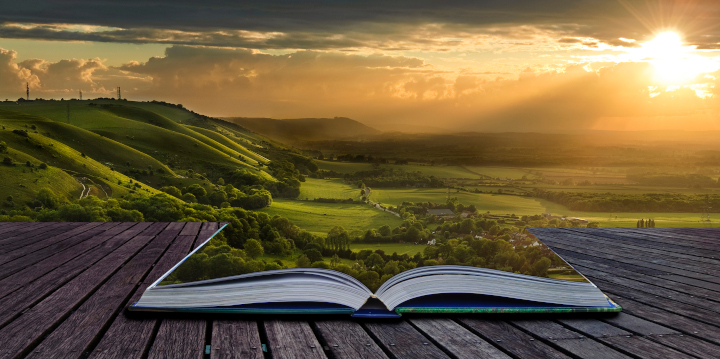
Photo purchased from … www.depositphotos.com
A commercial printing client of mine produces approximately one to three book titles each year. She and her husband value the production qualities of their print books (as do their clients), so the final copies are produced via offset lithography on 12 pt. cover stock with a 60# text sheet for the interior book block as well as French flaps and a hinge score parallel to the spine.
Along with these copies (1,000 or 1,500 for the initial commercial printing), my client produces about 50 galley copies digitally (on HP Indigo equipment or comparable, depending on the print supplier). These copies have 10 pt. covers without French flaps, and the text blocks are printed on 70# text stock.
That said, at the moment two different printers produce these books. One is more cost effective for digital (with a superb turn-around time). The other is a little pricey for offset lithography but can manufacture the books in five weeks (as opposed to the 16 weeks many other vendors are offering due to paper shortages).
The task, then, is to coordinate a digital and an offset press run at different printers and make sure the two books go together.
Issues That Have Arisen: Matching Digital and Offset Output
Matching digital and offset printing for the text and cover, in general, is a huge if not impossible task. In my client’s case, though, there will be no problem, since the text of the books is black only without halftones printed on a rough textured sheet. And even though the covers will be printed digitally (for the galley copies) and via offset lithography (for the final version), the galleys are only review copies and therefore don’t need to be of the same high quality as the final print books.
In your own work, however, you may have problems matching the look of digital printing and offset printing (both the color and the overall surface feel and look of the ink or toner). The key problem is that digital printing uses toner on paper (for laser printing) or a thinner ink mixture than offset inks (for inkjet printing). So even if the paper is the same, the look may be different.
So what can you do? You can standardize the paper (text and cover) used in the two versions. Then, before the final deadline you can get digital proofs on the papers of choice (so you’ll see the texture). Short of running a press proof (an expensive proposition for only a few copies of an offset printed cover), you can look closely at similar covers produced via offset lithography to get a general idea of how your digital and offset books will look together. You will probably need to make allowances for some difference (as my clients have learned), but depending on why you’re printing both a digital (laser or inkjet) version and offset version of your book, this may not be a problem (as it is not for my clients). Just choose offset for the higher level and digital for the lower and don’t expect an exact match.
Another option would be to offset print all the covers (in my client’s case both the galleys without French flaps and the final books with French flaps). Then the interior of the books can be either offset printed or digitally printed. The high-value text blocks will contain a little denser type than the digitally printed version, but the covers will be the same (except some may have French flaps, like my clients’ book).
In either case, in my experience it’s better to review both laser and inkjet samples before you decide. Inkjet seems to have superior color. Then again, the HP Indigo press, for instance, provides stellar color and coverage with laser technology (minuscule toner particles in a fuser oil).
For me, the takeaway is to look closely at laser, inkjet, and offset printed samples to see what you can expect.
Issues That Have Arisen: Preparing Covers
I sent both the cover designer and the text designer a list of specifications for the two jobs. The text in both cases was to be 256 pages. In one case (the final books), the text paper was 60#; in the other case (50 galley copies) the text paper was 70#. Therefore, the thickness of the spine needed to be different for each version (256 text pages of 70# stock are thicker than 256 pages of 60# stock).
The cover designer didn’t think about this. He assumed both text blocks would be the same because they had the same page count. Therefore, to fix the problem one cover art file had to be adjusted and resubmitted. To make this clear to the cover designer, I had received a complete cover template from one book printer and just the spine width (without a complete cover template) from the other.
In your own work, ask the printer for a complete book cover template with the back cover on the left, attached to the spine in the center, attached to the front cover on the right. These templates will also show where to position type on the spine (and how much room to use for text on the spine to avoid having anything wrap onto the front or back cover). Plus cover templates show required bleeds. Personally I find these invaluable. The book printer computes and automatically draws them based on the size of your book (5.5” x 8.5” in my client’s case), the page count, and the thickness (in pages per inch) of your text paper.
Check your proofs, but first, to avoid error, follow the cover template religiously.
Issues That Have Arisen: Bleeds
My client’s cover designer prepared two covers: one with and the other without French flaps. For the galley version (digital), he omitted the flaps but neglected to add bleeds. When I explained to him that live matter art either ends before the page trim or extends 1/8” past the trim for bleeds, he understood and revised the artwork for the galley-version cover.
Issues That Have Arisen: Photo Format
The text designer wanted to add one black and white photo (provided originally as a color image). She asked me if an RGB JPEG would be acceptable. This is what I told her. In making the PDF from the InDesign file, the software can convert images from RGB to CMYK automatically (not a problem in her case, since the photo would be black ink only).
However, in your own work, if you’re converting automatically from RGB (used for computer screen images) to CMYK (used for commercial printing), there can be unexpected color shifts in the translation. If you make the conversion to CMYK yourself, at least you will see the color shifts before the proof.
Regarding TIFF vs. JPEG, JPEG is a “lossy” file format (i.e., the compression algorithm). It provides a smaller file than a TIFF, but over multiple changes to, and savings of, the photo file, the JPEG will lose picture information. This doesn’t happen with TIFFs (which are “lossless”).
In your own design work, you can use either workflow. An RGB JPEG (which used to trigger the printer’s sending the file back to you for correction) can in my understanding now be automatically converted in the transition from InDesign format to PDF format. Ask your printer to be sure. And consider what you may lose when not making this change yourself.
That said, since RGB has a larger color gamut than CMYK, it’s smart to make all color changes in RGB first, and then convert the images to CMYK. Personally I like TIFF more than JPEG, since there’s less risk of lost (visible) picture information. I also like to distill files into PDFs rather than submit them as native InDesign files. Therefore, I prefer to place CMYK TIFF images in InDesign and then distill press-ready PDFs to hand off to the printer.
Issues That Have Arisen: Workflow
The printer with the digital workflow (for the galley copies of my client’s print book) works with InSite. InSite allows for file uploading, proofing, file approval, and probably other actions as well. I don’t believe it has preflight capabilities. (Based on my research, preflight actions seem to be applied in Prinergy, and then the results are brought into InSite.) But at least it provides an online portal for all reviewers to check and approve the accuracy of the files.
(A commercial printing vendor I’m working with on another job at the moment just sent me PDF proofs with bleeds and trim–a red rule around the pages—for a series of flyers. This is another workflow option some printers use–i.e., much simpler than InSite. I’m not sure what the book printer producing the final version of my client’s book—the one with French flaps–will send yet.)
That said, uploading files to InSite seems to be a little bit more complex (until you learn the process) than just using a printer’s FTP file upload site. In my client’s case, however, one reason the price and schedule are so good is that everything is automated. The other book printer (for the final version) charges more, and is producing the final version of the book via offset lithography. The third printer I mentioned (for a separate client’s flyers), who just sent PDF proofs, illustrates a PDF (virtual proof) workflow distinct from InSite.
So, in your own work, decide whether you need hard-copy proofs or digital (virtual) proofs. With my client’s printer’s InSite option (for the discounted price), everything has to be digital/virtual. (There are no hard-copy proofs in this workflow.) For the printer producing the final version, I have requested a hard-copy cover proof (and a virtual text proof). This way (for the more crucial of the two print book versions), my client will see a high-quality proof of the cover. In this case a hard-copy proof is important. And my client is paying more to get it.
In your own design and print buying work, decide first whether you need a virtual proof or a hard-copy proof, and then ask the book printer how he can accommodate you.
This entry was posted
on Sunday, September 11th, 2022 at 8:15 pm and is filed under Book Printing.
You can follow any responses to this entry through the RSS 2.0 feed.
Both comments and pings are currently closed.