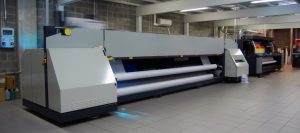
Photo purchased from … www.depositphotos.com
To reverse the common maxim, “Every silver lining has a cloud.” This also holds true for digital custom printing, the relatively new technology that has brought to commercial printing both a much wider color gamut than offset printing and the ability to make each printed piece different from every other piece in the press run.
Digital printing is wonderful. However, it has some pitfalls. And the best way to proceed is to consider ways to approach your print job to sidestep these potential flaws.
To begin my research for this article, I Googled “digital printing flaws” and found this article: “What Are The Common Flaws Of Digital Printing,” Hurricane Valley Times, by Kashif, 09/13/21. Here are a few of the limits the article notes (if you Google “digital printing flaws” or “limits of digital printing,” you will find this and many other helpful articles):
Speed and Cost
Digital printing is significantly slower than traditional offset commercial printing. For instance, an offset press might print a random job at 18,000 28” x 40” sheets per hour, with multiple copies of the job laid out on a single press sheet. On a digital press (let’s say an HP Indigo press printing on a slightly smaller than 20” x 28” press sheet), the top speed might be 4600+ sheets per hour. The Indigo sheet is smaller (some are closer to 13” x 18”), so the number of copies printed will be fewer than on a 28” x 40” sheet in an offset-printed job. Plus, in this example, the digital equipment is running at less than one-third the speed of the offset equipment.
So to paraphrase Kashif’s article, long runs printed on digital equipment are expensive (assuming time equals money).
Now my example above singles out high-end laser printing (also called electrophotography). There’s also inkjet technology, or more specifically web-fed production inkjet technology. In this case the equipment operates at approximately 600 feet per minute (based on sales literature from Ordant Technology referencing 4-color inkjet commercial printing). In this case the print heads span the width of the roll of printing paper (that is, the printheads image the whole sheet at one pass).
My math says this is close to 36,000 feet per hour (divided by approximately 2 feet for a 25” x 38” offset press sheet, or comparable to 18,000 sheets per hour on an offset press, give or take). So digital production inkjet on a web roll comes much closer to the speed of a sheetfed offset press than does HP Indigo digital laser printing.
So What Can We Learn from This?
Digital printing is ideal for short runs (much cheaper than offset). Check with your printer about the cut-off point (offset vs. digital) for your particular job. But don’t try to do all print jobs with a single technology. Play to the strengths of each. Digital can also produce variable-data custom printing. Offset printing cannot. Every sheet that leaves an offset press is the same, but you can vary each sheet leaving either an inkjet digital press or a laser digital press.
Ink Limits and Paper Limits
Particularly if you use production inkjet technology, you have to think about how the ink on a digital press interacts with the paper. The toner of laser printing (both the oil-based liquid inks the HP Indigo uses and dry toners) sit up on top of the paper. In offset printing, the inks seep into the paper at least somewhat (depending on the paper coating or lack thereof—uncoated book paper vs. coated text paper, for instance).
If the ink sits up on the surface of the paper, and you cover the press sheet with large amount of toner and then fold the paper stock (let’s say you’re printing a brochure with a heavy-coverage solid), the toner will crack at the folds.
In my experience, inkjet can cause the opposite problems. Since inkjet ink is very thin compared to the thick, tacky ink used in offset commercial printing, the inkjet ink can seep into the paper too much, and images (in particular) can look washed out or mottled. The paper composition is very important. In fact in prior years only special papers with special coatings were qualified for inkjet printing. Now I’m reading about more and more papers that will not soak up too much inkjet ink. There are more options, but this is still a consideration.
Other problems with ink include banding (uneven laydown of toner in large areas of a solid color) and inaccurate registration due to the paper’s skewing or due to digital press misalignment.
So What Can We Learn from This?
Printers have had a long time to perfect offset ink composition. They can make ink (and especially halftone dots) sit up on the surface of a press sheet while seeping into the fibers just a little.
In contrast, digital inkjet and laser printing are relatively new, and balancing heavy ink or toner coverage with good toner adherence to the paper (without the ink’s or toner’s cracking) is a challenge.
So talk with your printer early in the digital printing process, and ask about avoiding digital ink’s or toner’s cracking by scoring the press sheet prior to printing. Also ask about how best to compose the inks and toners to allow for good opacity. Digital inks (inkjet inks) are much thinner than offset inks, so they are less opaque. Therefore, it’s important to get enough ink on the press sheet to create consistent, even, thick solids.
This might involve creating mixes for black ink that include cyan, yellow, and magenta as well as black. Or it might involve laying down white digital ink or toner under the process colors. (This will ensure the opacity of the thinner digital ink/toner and keep the darker substrate–if you’re using one–from changing the color of the overprinted inks.)
All of this points toward your involving the printer early in the process. You may even decide to omit heavy solids in your design for digital printing, or you may choose printing paper that is more ideally suited to your goal.
You may even want to discuss lamination options with your printer, depending on which laminates will adequately adhere to digital ink/toner. This may keep the inks from fading quickly (since they are more susceptible than offset inks to color degradation in sunlight).
Color Accuracy and Color Consistency
In offset printing, the pressman overprints screens of cyan, magenta, yellow, and black ink to simulate full-color printing. This reproduces most colors but not all. If you have a specific color that is “out of gamut” but that you need to use for a corporate logo, you have to add one or more PMS colors.
With digital printing, you don’t add PMS colors. However, many inkjet presses do use expanded color sets (some with red, green, and blue; others with green, orange, and purple; still others with light versions of cyan and magenta). These expanded color sets widen the color gamut of digital printing way beyond that of offset printing.
That said, if your color is critical and you’re printing digitally, you need to watch for inaccurate color. This could be due to printhead problems (on inkjet equipment) or a number of other causes. This might create problems if you’re trying to match the color in other printed products (or trying to match offset-printed work to digital printed work, for instance).
In these cases your best solution is to request color proofs and check them under pressroom-comparable lighting conditions (5000K, which is the color of sunlight). Using the same press for repeat jobs also helps (which is why it’s smart to get a complete, new proof if you change digital printers or presses for a reprint job, and then match this proof to your original press run).
This entry was posted
on Thursday, November 18th, 2021 at 1:24 am and is filed under Digital Printing.
You can follow any responses to this entry through the RSS 2.0 feed.
Both comments and pings are currently closed.