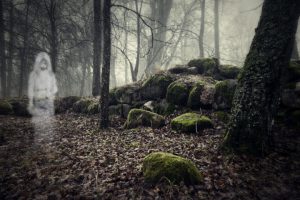
Photo purchased from … www.depositphotos.com
What Are Ghosts?
Ghosts are scary things. Well, maybe not so scary in commercial printing, but they are extremely frustrating and time consuming to eradicate, and a pressman’s ability to remove ghosts demonstrates the knowledge base that makes him an artist and a craftsman.
First of all, what are ghosts? They are unplanned images from elsewhere on a press form that show up on your press sheet. They are always a repetition of something already on your plate, either text or an image. In my experience they usually appear as a lighter image in a solid area, but sometimes they appear as a darker image within a lightly screened area.
In certain press layouts the potential for ghosting is higher than in others. When it happens, it is usually because the necessary confluence of layout problems has been missed in prepress, plating, and even the pressroom.
Ghosting is a result of ink starvation, which is a result of the size of the commercial printing press and the placement of heavy-coverage solid ink on a press signature. For instance, I once designed a poster which included text, a large vertical photo, and a solid ink border surrounding the central image. The border bled off the poster on all sides. If the prepress department had not flagged the job initially, it could have caused problems.
Without alteration, as the poster press sheet (in this case, with only one poster on a sheet) traveled through the press, the press would have deposited a lot of ink on the top of the poster, where the heavy coverage border printed all the way across, and then relatively little along the sides of the poster’s border, and then a lot of ink where the bottom of the border ran through the press (with solid, heavy PMS ink all the way across the custom printing plate).
In simpler terms, the press shifts from a heavy deposit of ink to a lighter one and back to a heavier one. And sometimes the result is the faint (maybe 20 percent of solid) ink markings (lighter or darker than the surroundings) repeating an element from another part of the layout.
So What Can You Do?
I have seen such a dilemma resolved in three ways. The first, quickest, and cheapest way is to catch the problem before the job leaves prepress. Stopping the press and making new plates takes time and costs money. Avoid this whenever possible.
The second option is to add “take-off bars,” or “ghost bars,” to the sides of the poster (i.e., add a solid laydown of ink outside the image area of the poster on the press sheet). The ghost bars widen an area printed in heavy ink and make it more equal in size or total area (i.e., equal in the amount of heavy ink coverage) to the opposite dimension (width vs. height).
This avoids the quick shift from using lots of ink to using very little ink to using lots of ink.
Granted, ghosting can be far more elusive. In my case the ghosting (which was avoided) would have been just an unevenness in ink coverage on the vertical and horizontal segments of the border surrounding a photo. In other cases, bits and pieces of large display type or photos can appear where they are unwanted. The culprits are usually heavy solids, screens, large areas of type, groups of halftones, and reversed type (i.e., areas with a lot of ink separate from, but on the same press sheet as, areas with far less ink). So the best thing to do if you’re at all concerned is to ask your commercial printing supplier about the potential for ghosting.
To get back to my own press inspection and discovery of ghosting, the printer I was working with did something else, something I hadn’t seen before and haven’t seen since. He tilted the poster on the press sheet. What this did was even out the laydown of ink on the press sheet and thereby avoid ink starvation. Due to the tilting of the entire poster, there was a more gradual shift from heavy ink coverage to light ink coverage and back to heavy ink coverage in printing the border surrounding the photo.
Similar Problems
Like ghosting, other ink density problems can occur during a press run. And the human eye is most unforgiving in these cases.
For instance, large areas of solid color can look uneven. The same is true for screens of color. A small press, according to Getting It Printed, by Mark Beach and Eric Kenly, starts to have problems when the size of the solid or screen exceeds 3” x 3” (and when the size of large type exceeds 72pt). A large press can hold consistent density for a solid or screen for a 9” x 9” area. So sometimes moving to a larger press will fix the problem of an uneven screen or ink solid.
But sometimes even this is not enough.
One way to rectify such uneven density is to print two “hits” of the same color, one over the other. This evens out the coverage. Another option is to print a screen of a color and then cover this with a solid pass of the same color. A lot of printers do this for a heavy coverage of black ink. Or, a commercial printing supplier may build a “rich black” using not only black ink but also certain percentages of cyan, magenta, and yellow ink. This can yield richer coverage and more consistency of color.
This struggle to maintain consistency in ink coverage can also occur in background screens that must be consistent from page to page (or, worse, from press signature to press signature). This is particularly problematic for neutral colors (close to gray but with a slight color cast). Since the human eye can perceive even small differences in color on pages laid side by side, printers often sidestep the potential problem by adding an additional PMS color for all large background screens that repeat (particularly from press signature to press signature).
Further problems of a similar nature can occur with “in-line” colors on a press sheet. Imagine a press sheet with four pages across the top and four pages immediately below these (eight on one side of the form and eight on the other), yielding a sixteen-page press signature. Now imagine that this is part of a magazine, with heavy-coverage solids, screens, large type, pages on the signature with very little type and large expanses of white paper, and other pages with multiple printed elements.
Mentally “scan” across and down, from the pages above (four across) to the pages below. If there is a shift in either ink density or color from the pages entering the press first to those immediately below them and therefore “in line” on the press sheet, there can be visible color casts. For instance, a heavy-ink-coverage advertisement in a magazine may either take on a color cast, or cause an in-line page to take on a color cast (maybe a reddish tinge, if the large photo in the ad includes warm flesh tones).
In this case the pressman may have to adjust the color across the sheet to compromise or just make the paid advertisement perfect while tolerating less than perfect color in the in-line page. (Keep in mind that the ink density can be adjusted from one side to the other across a press sheet, but in the direction the paper travels through the press (usually the wider dimension on a sheetfed press), anything that lines up along this axis will have equal-density ink coverage. And the only way I know to remedy these problems is to impose the pages differently on the press sheet, usually by producing smaller press signatures (which would require more press runs).
This entry was posted
on Tuesday, September 7th, 2021 at 5:20 pm and is filed under Printing.
You can follow any responses to this entry through the RSS 2.0 feed.
Both comments and pings are currently closed.