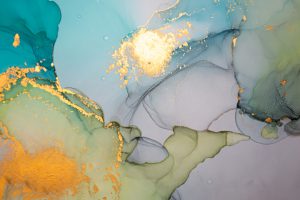
Photo purchased from … www.depositphotos.com
Nothing shines like gold. Nothing is as opulent. So when you print an invitation to a classy event, or you design a business card for an upscale customer, consider adding the luster of this metal to your print product.
That said, commercial printing of metallics does have its challenges, shall we say, but it’s worth it. It really does make an impression.
Offset Printing Metallics
First of all, gold ink is not really gold. It is composed of flakes of reflective metal (actual metal) such as zinc, copper, aluminum, or bronze (depending on whether you’re creating a gold look or a silver look) suspended in the vehicle, or fluid part, of the ink. Because of this, it can flake off, or it can tarnish. Therefore, it’s essential to print on a gloss coated stock and coat the sheet after the custom printing process with an aqueous or UV coating. The reason for choosing the coated sheet is that the ink sits up on the surface of a coated sheet (more effectively on a gloss than matte sheet) and does not seep into the paper fibers as much as with an uncoated sheet. (This is called ink holdout.)
(Personally, I’d also ask your commercial printing vendor about the chance that the specific coating may adversely react to the metal and foster tarnishing. I know that a press varnish will yellow over time, and this could cause problems as well. So also tell your printer how long the printed product needs to last. Is it a promo piece that will be received, looked at briefly, and discarded, or does it need to look good for a long time? You may even want to ask about shelf life if, for example, you’re printing 1,000 business cards. You don’t want the last 500 copies to look tarnished.)
Metallic ink (whether gold or silver, or even a metallic blue or red, which are currently in vogue) is not one of the process inks (cyan, magenta, yellow, and black). So you will need an extra unit on an offset press, which will also cost a bit more. The additional spot ink, which will fall into the category of a PMS Metallic Ink, will need its own printing plate. It cannot be combined with the process color screens to create another hue.
All of this presumes you have chosen offset custom printing, although I would assume that any of the other traditional, analogue printing methods, including rotogravure and flexography, would treat the ink separation (and plating) process the same. So talk with your print provider about how you need to set up the art files using InDesign to ensure that the gold, bronze, copper, or whatever other color you choose winds up on its own plate.
Finally, don’t assume that every printer knows how to do a good job printing metallics. It is a skill, an art. Request printed samples to make sure you’ll be happy with the printed result. Also, you may want to pay extra for an actual press proof if the job is very high profile. Expect this to be expensive. You’re essentially paying for a separate press run (albeit on a small press). But for the right project, it may be worth it.
So what can you use metallics for? They’re great for a logo (but do keep in mind that if you start off with metallics on a logo, you’ll need to print them—at a premium—each time). Again, this may be worth it for the “Wow” factor. On brochures, they can highlight text or line art. They can make stationery look sophisticated. And if you use a six- or eight-unit press, you can add an additional metallic for a special graphic treatment (CMYK plus two metallics, for instance).
Again, all of this is based on traditional offset lithography, which is only one of several options.
Foil Stamping Metallics
Let’s say you want to print a special invitation in silver ink on a black uncoated paper. If you used traditional offset lithography, the vehicle of the ink would seep into the paper. Most probably the metallic ink would wind up being uneven (not of the same consistency on all portions of the text or imagery). This could look like a serious mistake on the final (expensive) print run.
So what can you do? You can skip offset commercial printing and produce the invitation using foil stamping. Your print provider would first have a metal cutting die made for all text and line art. Then, using a foil stamping press (an impact printing press rather than an offset press), the printer will foil stamp the front and back of the black paper invitation using heat and pressure, providing an even layer of type and graphics impossible to achieve (in this case) only using ink on paper.
But you’ll have to pay extra for the stamping die, which will be subcontracted out by the printer and which will therefore add time to the custom printing process.
Foil stamping does, however, tend to look spectacular, and the text and graphics are far more likely to be of consistent density on even an uncoated paper. Plus the look of the type and graphics will be even more glossy than with metallic ink.
Also, you can have the printer laminate (maybe a soft-touch laminate) the job to add extra thickness, protection, and an interesting feel.
That said, it’s wise to get printed samples from your vendor, because this is skilled work that not all print providers can do well.
Digitally Printing Metallics
Gloriously, we now live in a digital age, and there’s no lack of metallic and foil simulations available if you are not ready for the expense of foil stamping and your design doesn’t lend itself to the less expensive option of offset lithography.
Here are some companies you may want to research:
Indigo: Hewlett Packard and Indigo Ink have been working on digital metallic options, including a metallic silver that can be used as a spot color (for separate text, line art, and such), and can also be printed under the CMYK toner for a multicolored, metallic appearance or a metallic sheen on any distinct CMYK color build.
Keep in mind that this is a toner-based print product (toner particles suspended in a liquid oil base). However, I have personally seen incredible results, a dramatic color gamut, and incredible resolution—plus the variable data printing capability of a digital-only workflow.
In addition, be mindful that the metallic look is more matte (less glossy) when compared to foil stamping. But you can include an unlimited number of metallic effects on the same press sheet. And you can use uncoated paper. Plus it’s cheaper than the other options, and it’s variable data commercial printing.
Scodix: According to my reading, Indigo Ink can print a coating under the CMYK toner particles to achieve their striking look, but (in contrast) Scodix Metallic can add a clear polymer coating over the CMYK inks to achieve spectacular color effects. Scodix also offers foiling capabilities as well as embossing capabilities, so you could conceivably include all of these plus multiple metallics in a single printed product. Plus, an additional Scodix SENSE coating can protect the underlying image from scratches and scuffs, something not possible with traditional foil stamping.
Keep in mind that all of this is digital. There is no metal die-making (as in foil stamping or traditional embossing), and you can vary the image from one print to the next. If you look closely, though, you will see that the process is an additive manufacturing one, with the polymer coatings built up on top of the press sheet (i.e., with no indentation on the back of the press sheet as with traditional embossing).
What you get from this technology, among other things, is the ability not only to vary printed products from one unit to the next but also to inexpensively produce single prototypes. You can make an accurate model of a high-end marketing piece (or even a special packaging initiative for cosmetics, for example). Then, if the client likes it, you can roll out the rest of the print run. Or you can make changes and then roll out the job. You definitely can’t do this with traditional analog processes without spending a lot of money and time.
Vivid3D: I received a sample from a binder and presentation box company recently showcasing multilevel sculpted embossing (with no indentations on the back of the sheet); transparent blue, silver, gold, and clear foil effects; and something called “splash,” which looks to me like reticulating varnish (a textural, patterned effect). All of this is on the same press sheet. None of it requires die-making. Wow.
So if you do nothing else, check out Scodix, Indigo, and Vivid3D. I’m sure there are more hot companies as well. You may also want to search for “digital enhancement.” I think that’s a good starting point. And you’ll have a world of options for all budgets, between these and the traditional analog processes of offset lithography and foil stamping. Good luck. Don’t look back.
This entry was posted
on Wednesday, July 28th, 2021 at 3:46 pm and is filed under Inks.
You can follow any responses to this entry through the RSS 2.0 feed.
Both comments and pings are currently closed.