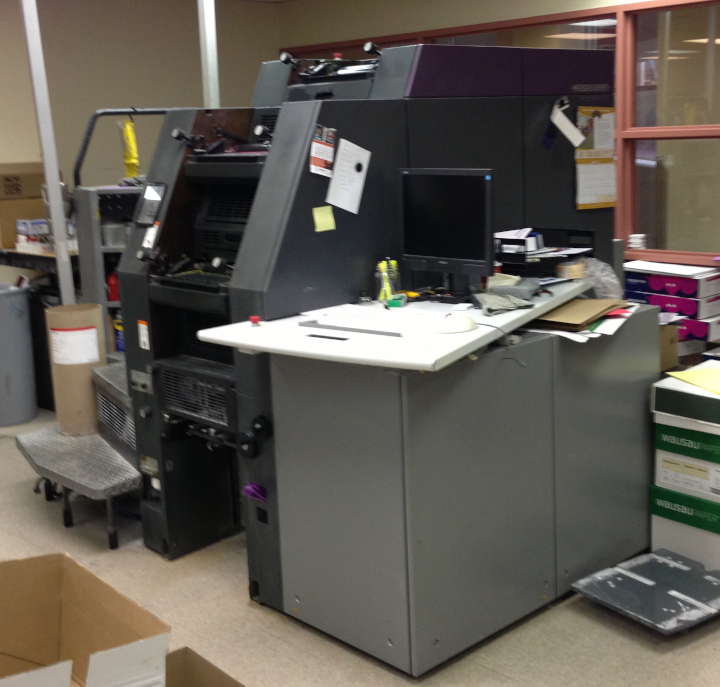
Photo purchased from … www.depositphotos.com
When a printing supplier I work with mentioned that she had a Heidelberg direct imaging press for one of my client’s jobs, a collection of “chin cards” based on her color model for selecting complementary hues for make-up and clothing based on a person’s complexion, I was thrilled. Unfortunately, I was also mistaken. The press turned out to be a Heidelberg, but it was a production-quality color laser printer, not a waterless press.
That said, when my associate mentioned the press, I remembered seeing the Heidelberg Quickmaster DI in the late 1990s and early 2000s. I had been amazed by its dense ink coverage, halftones upward of 300 lpi (with no visible rosette patterns), super-hard halftone dots, and incredible color fidelity.
The Heidelberg Quickmaster DI and Waterless Offset Printing
First of all, Heidelberg is known for exceptionally high-quality manufacturing in the commercial printing press world. Color fidelity, durability–Heidelberg is the BMW of presses.
That said, I supplemented my own exposure to waterless printing on the Heidelberg Quickmaster DI press with online research (including Wikipedia), and then I reviewed online literature by Heidelberg and came up with the following.
The Quickmaster DI is a waterless press. This process has also been branded as “Driography” (by 3M in the late ‘60s). It differs from offset lithography in the following way.
Offset lithography is based on the fact that oil and water do not mix. By coating the printing plate (during commercial printing) with a water- and alcohol-based dampening solution that is attracted to the non-image areas of a metal printing plate, and by attracting the oily offset inks to the image areas of the printing plate, it is possible to have both ink and water on the same flat surface of the plate (called a “planographic” surface) while only printing the ink from the image areas (type letterforms, halftone dots, and solids).
In contrast, a waterless press starts with a metal plate that is coated with silicone rubber. A digitally-controlled laser burns the plate, activating a photo-polymer that allows the silicone (during the processing of the plate) to slough off from the image areas only (type and images), leaving the remaining silicone coating intact. Silicone then repels the ink (of a specific viscosity), but the exposed metal of the underlying commercial printing plate attracts the ink (of a specific viscosity).
Because of the surrounding silicone, the image areas of the custom printing plate are actually recessed (also known in both fine art printing and commercial printing as “intaglio,” with the third option, after “planographic” and “intaglio,” being “relief” or raised printing—like letterpress).
Because the image area is recessed, when compared to offset lithographic plates, a waterless press can carry more ink to deposit on the printing substrate. So ink density can be much higher than in traditional offset lithography.
More Benefits of Waterless Offset Printing
First of all, it’s not really offset lithography because it’s not based on the mutual repelling of oily ink and water (which is more of a chemical process). Because of this, waterless offset (which is more of a physical process) is actually more precise than offset commercial printing, in part because pressmen don’t have to struggle to get the correct balance between the oily ink and the alcohol and water dampening solution.
Here are some more benefits:
- Waterless inks are more viscous than offset inks. That means they are thicker and tackier (they stick to each other better than offset inks, which improves ink trapping—or the slight overlapping of inks where they abut to one another). Waterless inks provide a wider color gamut and greater color fidelity than traditional offset lithography inks.
- The higher halftone screen rulings–from 300 lpi (lines per inch) to 800 lpi or higher, in contrast to the 175- to 200-line screens used for traditional offset lithography–allow for more detailed images and increased ink contrast.
- Since waterless plates can carry more ink, and since the ink is thicker than offset inks, there is better ink holdout with waterless printing than with offset lithography. (An ink’s holdout is its ability to stay on the surface of the paper rather than seep into the paper fibers.) In addition, the lack of water absorption by the commercial printing paper also contributes to this enhanced ink holdout. (That is, wet paper reduces ink holdout. Drier paper increases ink holdout.)
- The thicker ink and absence of a water and alcohol dampening solution also maximize the dimensional stability of the paper. Drier paper doesn’t stretch as much as wet paper. This makes for better registration and less waste.
- On a traditional offset lithographic press, you can print from (approximately) a 5 percent halftone dot to a 95 percent halftone dot. Anything lighter than 5 percent would be white (unprinted paper). Anything darker than 95 percent would be black. (Granted, these numbers will vary depending on the press, the ink, and the paper). That said, for waterless offset, the printable halftone dots range from .5 percent (in highlights) to 99.5 percent (in shadows). In short, waterless offset allows for a much larger printable tonal range than traditional offset lithography.
- Color is more consistent (i.e., more easily maintained) throughout the press run.
- Waterless halftone dots print with a harder edge and little or no fringing, elongation, or dot gain when compared to offset lithography. This allows for crisper images and more detail in highlights and shadows.
- The waterless offset process speeds up printing, reduces waste, and eliminates environmentally hazardous chemicals. More specifically, since the overall process is more precise, it can proceed more quickly with less waste (paper waste, ink waste, etc.). And since the dampening solution is no longer necessary, no alcohol or waste water is released into the environment.
- Since the process is simpler and more consistent than offset lithography, waterless offset cuts makeready time in half when compared to offset lithography.
- Plates for a waterless offset sheetfed press can last for 100,000 to 200,000 impressions. And on a web-offset press, the printing plates can last for 300,00 to 600,000 impressions, although rougher papers (below a #1 or #2 coated press sheet) will reduce the run length of the plates.
- For repeat press runs, you can save the digital ink-key preset information, allowing for the press’ “coming up to color” and yielding usable press sheets much faster than with offset lithography.
- Finally, if the waterless press is a Heidelberg Quickmaster DI (direct imaging) press, then the plates themselves can be imaged right on the press. I’m sure by now there are other direct imaging presses as well. My experience with this particular technology (as reflected in the Heidelberg press) came quite a while ago in the late 1990s and early 2000s.
The Caveat: Temperature Control
For better or worse, there’s one caveat. The process is based on the temperature of the inks. For the inks to stick to the exposed part of the plates, they can’t be too hot (which would reduce their viscosity). Therefore, waterless presses need to have a coolant (water) pumped through tubes in vibrating rollers in contact with the inks to reduce their temperature (as it rises during the printing process) and keep it within a usable range.
Without such cooling devices, the lack of water in waterless offset would allow for increased friction between plates, rollers, and ink (as would the milling of the ink itself through the rollers), raising the temperature of the ink. And this increased temperature would change the viscosity of the ink and therefore cause printing problems (i.e., it would reduce the clear separation between ink avoidance and ink affinity–away from the silicone coating and toward the exposed metal plate). With the cooling systems, this is not an issue.
Why Now? Why Not in the 1960s or 1970s?
With all of these benefits, I personally wondered why the technology didn’t catch on earlier, say in the ‘70s or ‘80s. Based on my research, it seems that there were some issues with paper, plates, press, and inks. Apparently these have been resolved, and with more aggressive advertising this technology has started to come into its own.
The Takeaway
So waterless offset is really more of a mechanical process than a chemical process. It yields incredible color as well as superb halftone detail and contrast. Therefore, if you have a press run from 500 to 25,000 units or considerably more (up to 600,000 units), you may want to do some research into which commercial printing suppliers have this kind of press (or which printers have configured some of their presses to do both waterless and conventional offset lithography).
This entry was posted
on Monday, June 12th, 2023 at 12:18 am and is filed under WaterlessPrinting.
You can follow any responses to this entry through the RSS 2.0 feed.
Both comments and pings are currently closed.