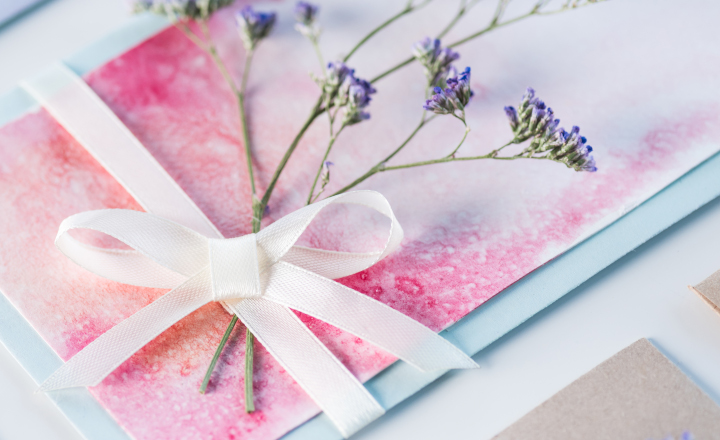
Photo purchased from … www.depositphotos.com
I’m a great believer in marriage. Weddings give you an opportunity to use one of the most artistic printing techniques (as well as one of the oldest) in existence: engraving. In fact, since my fiancee and I teach art to autistic students, I could very well share this same information with our students, because there is a long history of engraving in the fine arts as well as the graphic arts.
Engraving is an art form that lends itself to special occasions, such as weddings. However, it is also quite appropriate for corporate materials such as invitations to special gala events, letterhead, and business cards.
The Engraving Technique
Engraving is the opposite of letterpress. In letterpress, raised image areas and text print content onto commercial printing paper. In engraving, lines of images and text are incised into either steel or copper printing plates. Thick ink is wiped onto the plate and then wiped off, leaving ink only in the incised image areas.
Keep in mind that the dimensions of the engraving work tend to be very small (such as the size of a business card or invitation). When the intense pressure of the engraving press is applied, it forces the custom printing paper into the incised type and image areas of the inked plate, and the paper absorbs the ink. At the same time, the image areas are raised slightly by the intense pressure. So when the final piece comes off the press, the back of the sheet is slightly indented behind the typescript letters, and on the front of the sheet these very same printed elements are raised.
To compare this to the most common current form of commercial printing other than digital printing (i.e., offset lithography), offset printing plates are flat (neither raised like letterpress nor lowered, or incised, like engraving). In offset printing, what keeps the ink confined to the image areas is a chemical property of oil and water (or oily ink and water). That is, oil and water do not mix, so it is possible to separate them on a flat commercial printing plate.
To compare all three custom printing techniques in this light, engraving is an “intaglio” (recessed-image) printing process, offset lithography is a “planographic” (flat-image) printing process, and letterpress is a “relief” (raised-image) printing process.
Beyond the aesthetics of a special business card or invitation, engraving provides the sharpest printed impressions of any custom printing technique. Therefore, it is used to print currency and stock certificates as well.
Engraving plates are either steel or copper. According to my go-to book on printing, Mark Beach and Eric Kenly’s Getting It Printed, steel plates will allow for much longer press runs than copper plates. (Copper plates are usually good for press runs up to 5,000 copies, and then they deteriorate.) However, engravers usually only offer a few typefaces on steel plates.
Engraving plates can be imaged in the following ways:
- The lines can be incised by hand using tools. (This is used for steel plates.)
- The type and imagery (very simple line drawings, for instance) can be chemically burned into the metal if you’re starting with a “mechanical” (hard copy, actual type and imagery pasted up on paper), which is pretty much an extinct option now. (This is used for copper plates.)
- The type and imagery can be burned into the commercial printing plate with a laser from digital art files (more common). (This is used for copper plates.)
When you’re designing for engraving, keep in mind that the inks are thick and opaque, which can make them a great choice for a darker paper stock. (They are more striking than transparent offset inks printed on darker commercial printing paper.) Also they come in gloss and dull formulations, which will give you options. For instance, the gloss inks may even appear a bit metallic.
One of the most important things to remember if you are buying engraving services is to choose an appropriate, high-quality paper that will showcase the aesthetics of engraving. Let your printer help you choose the paper stock.
Another thing to remember is to ask the printer to confirm the heat tolerance of your final printed product if you intend to print names and addresses on a laser printer. In some cases the high heat of a laser printer could damage the engraved product.
Engraving requires intense pressure, as noted earlier, so it lends itself to small presses printing small images. Getting It Printed notes that anything larger than a 4” x 8” area would require an additional pass through the press. (For instance, your printer may do one pass for the top of your letterhead and another pass for the bottom of your letterhead.)
An Option to Engraving
But what if you can’t afford the expense of engraving? Or maybe you want something for larger-format printed pieces. What are your options?
Thermography is a hybrid printing technique that actually starts with offset lithography. You may in fact have seen thermographically printed business cards and thought they were engraved, because the type and imagery are raised as in engraving. (One key give-away, however, is that the underside of the printing paper is not indented behind the type letterforms.)
Thermography starts with slow-drying offset printing inks that are dusted with thermographic resin powder after the offset printing step. This powder sticks to the offset ink and “takes on the color of the underlying ink, but may not match perfectly” (Getting It Printed, p. 138). Excess thermography powder (powder not covering type or other image areas) is then vacuumed away, and the printed piece is heated. Heat melts the thermography powder into the offset ink, but it also causes the powder to bubble up (hence the raised effect that simulates engraving).
In my experience, two things are important to remember with thermography. The first is to keep things simple. You can create an attractive, raised effect, but if you try to reproduce anything but the coarsest halftone screens, the screens may plug up and look uneven. (I personally did this once about thirty years ago, so I encourage you to learn from my mistake.)
Also, there is a chance of your receiving a printed piece in which the ink looks stippled (a pattern of tiny indentations, like the skin of an orange peel). So ask your printer for samples, and make sure he is skilled in thermography and can avoid this stippled effect. You want the powder to rise as it is heated, and you want a uniformly glossy appearance, so your printer must be able to control the offset ink application, heat, and thermography powder application.
That said, you don’t have to use thermography only for business cards or letterhead. Getting It Printed suggests applying thermographic printing to perfect-bound print book covers, for instance, perhaps highlighting the title of the book by making it colorful, raised, and textured.
If you choose thermography for a printed item, you have a choice of fine, medium, or coarse thermography powders, so you can use fine resign powder for fine lines and thicker granules for larger areas of type or color solids. However, too large an area of color thermography might result in a blistered appearance. Also, printing across a fold will result in cracking of the dried thermographic powder.
And finally, thermography does not have the highest rub resistance and can therefore be scratched. Also, thermographically printed ink does not tolerate the heat of a laser printer and can lose its “rise and luster” (Getting It Printed, p. 139) if heated.
This entry was posted
on Sunday, March 12th, 2023 at 4:55 pm and is filed under Printing.
You can follow any responses to this entry through the RSS 2.0 feed.
Both comments and pings are currently closed.