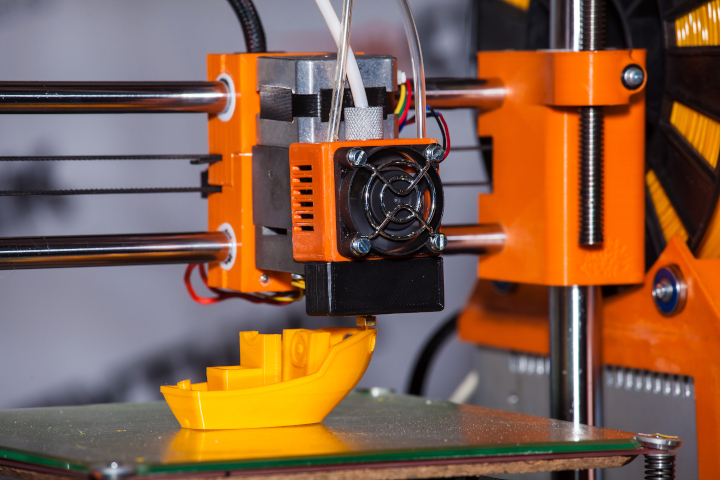
Photo purchased from … www.depositphotos.com
In these PIE Blog articles I haven’t discussed 3D custom printing very often because I have had trouble wrapping my brain around the technology involved. While I still do not really understand how these printers work, I recently became more interested when I read about how 3D printing has been used increasingly to marry the 6,000-year-old technique of lost-wax casting with the precision and relative ease of digital CAD (computer aided design).
The process is faster and less labor intensive than traditional injection molding, so the prices for the casting component of manufacturing can go down, while the precision of the “geometry” (the structure of a digitally produced graduation ring, for instance) can go up.
What Is 3D Printing?
First of all, as a general overview, 3D custom printing is a type of additive manufacturing (insofar as the material used is built up layer upon layer rather than ground away from a solid block of metal or plastic). There are various ways to do this using powders or filaments (like plastic string from a spool), but essentially the raw material is expelled through a heated jetting device (like inkjet printing) to create a three dimensional object on the moving build plate of the printer.
Depending on the technique and the substance used, this material can be hardened, or cured, by exposure to a laser, chemicals, or even UV light (just as UV commercial printing inks will cure when exposed to UV light). Or, powdered particles can be fused together (called sintering) by exposure to a laser to create the material for the final product. The constant thread through all of this is that the final item is more or less complete, more or less detailed, and more or less durable depending not only on the raw materials but also on the method used to combine them layer by layer into a physical object.
What Is Injection Molding?
Prior to 3D custom printing, manufacturing shops that needed to create a part (either plastic or metal) had to create an injection mold. The designer had to produce a 3D model (usually by carving it), then reproduce the inverse image of the model (i.e., a mold with an empty cavity in the shape of the final object).
At this point, molten metal or plastic could be poured through an access hole to fill the empty mold. Then, after opening the mold, the designer could remove the final product. This could be done multiple times as needed. As with all analog printing processes (to which you might draw an analogy), all of these injection molded (because the material had been injected into the mold) pieces were identical.
This took a long time (and therefore cost a lot) because the molds had to be tooled and ground to create each part (of, for example, a motor, with a large number of individual parts that had to be injection molded and then assembled). Also, the process was not as precise as it might have been, so it was necessary to grind or tool the component parts, removing any extraneous material (imagine a perfect metal bolt, but with little pieces of metal sticking out that must be ground off before it can be used).
What Is Lost-Wax Casting?
This is very similar to injection molding. A figure or model is created (carved, for instance) and then covered in wax (to the desired thickness of the resulting statue (let’s say a bronze sculpture). If the metal sculpture will be hollow, then a core can be added inside the wax model. On top of this model the designer slathers a thick layer of heat resistant plaster. Wax tubes like the limbs of a tree (these are called sprues) are added. These will create pathways through which the final metal can enter the mold and noxious gases can exit the mold. When the mold is inverted and then heated in a kiln, the wax turns to liquid and runs out of the mold through the pathways, leaving a negative (or inverse) image of the initial model.
Then, molten metal can be poured into the empty cavity in the mold. When this has solidified, the mold can be opened and the metal statue removed.
As with injection molding, some final grinding and machining work must be done on the final bronze casting.
3D Modeling, and the Marriage of Injection Molding and Lost-Wax Casting
Now, with the advent of 3D digital printing, the 6,000-year-old lost-wax casting technique can be used to make products (and especially prototypes and molds) accurately, efficiently, with precise detail, and with far less post-mold machining work on the final component pieces (let’s say a graduation ring, since it may include raised portions and incised lettering, or whatever other complex, multi-layered “geometry” or design work).
Using CAD (computer aided design) software, which in this case has been simplified and is therefore more user-friendly than complex, traditional CAD/CAM software, the designer can produce wax models on a 3D printer that can be covered in a mold-making material, heated to let the wax run out, and then poured with metal to produce the final molded components.
This is a much faster process than traditional injection molding. The process, from model-making to mold-making to final metal product or component item, can take days rather than weeks (often up to 12 weeks the traditional way). In addition, the process is much more precise (think about the multi-level design, filigree, and lettering in a graduation ring, for instance), so post-molding processes such as grinding are minimized when compared to more traditional “investment casting,” the contemporary version (without 3D printing technology) of lost-wax casting. Plus, you can easily make changes to the wax model (perhaps various iterations of the graduation ring design) with the CAD software and 3D print a number of wax images quickly.
Furthermore, it’s possible to produce prototypes quickly and then incorporate any revisions into the final model. Speed equals lower costs. And the resulting items are more detailed and precise, as well as significantly faster to produce using the marriage of lost-wax casting and 3D custom printing.
The Takeaway
For those of you who entered the commercial printing or graphic design trade because you’re artists, you may very well find it enjoyable to learn about processes that cross over from the fine arts to the graphic arts. (Keep in mind that Henri de Tolouse-Lautrec was a poster designer and illustrator as well as a painter, and Andy Warhol was an illustrator as well as a painter.)
Discovering ways in which traditional methods, such as lost-wax casting, have been incorporated into modern graphic design (and product design) can enrich your understanding of what you do in your day-to-day design work and why.
There are many more areas in which the fine arts and commercial arts overlap. These include collagraphy (adding various collage materials to build up a paper custom printing plate, then varnishing the composite whole to make the plate waterproof, and then printing the plate). And they even include carving a design in a styrofoam plate (the kind used for saran-wrapped pork chops in a grocery store) and then printing this as a plate (as my fiancee and I have done with our art therapy students).
In all cases, commercial printing depends on aesthetics, the appreciation and creation of beautiful items, as well as the selection of the quickest and most technically effective approach to making multiple copies of something—whether it is a two-dimensional print book page or fine arts etching, or a three-dimensional component part of a toy automobile engine, using lost-wax casting models produced on a 3D printer run by CAD software.
This entry was posted
on Monday, October 24th, 2022 at 12:58 pm and is filed under 3D Printing.
You can follow any responses to this entry through the RSS 2.0 feed.
Both comments and pings are currently closed.