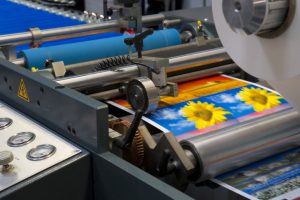
Photo purchased from … www.depositphotos.com
From all the hype online about digital this and digital that, you would think that only presses like the HP Indigo or Kodak NexPress were in demand–that offset printing was in its death throes.
On the contrary, there are very good reasons to choose offset commercial printing. Plus, there have been several advances in offset printing technology in the past several years that have made offset printing more efficient and less costly.
In reading the various articles on digital and offset custom printing sent to me each week by the Google aggregator, I came upon a piece by Jamie Neill, from GEW UV, published on 02/13/22. It is entitled “The Future for Sheetfed Offset?”
First of all, before we address the article, digital printing offers certain benefits.
If you are producing a short run of a job (let’s say 500 to 1,000 copies), digital is less expensive (total cost). Of course, if your job is a multi-page document like a print book, it’s best to discuss options with your printer first (after all, multiple copies of a multi-page book climb into the multiple hundreds and thousands of page clicks very quickly).
The reason short runs are better suited for digital is that offset printing requires a lot of set-up time, and digital printing requires almost none. So for long jobs your set-up time is spread over more copies. While the overall cost is higher, you get far more copies, so your unit cost is much less than for digital.
On another note, if you are printing a variable-data job, digital printing is best. Offset printing uses printing plates that reproduce the same image throughout the press run, so for offset commercial printing, variable data is not an option.
Benefits of Offset
That said, here are some benefits of the current state of offset printing technology, according to Neill’s article.
Presses are faster than they used to be. Make-ready processes are less time consuming because they have been automated in many cases. And overall press operations have benefited from automation as well (such as the electric-eye, closed-loop feedback systems that monitor press color in real time and then feed this information back into the computer so it can adjust color on the fly). In short, the offset printing process has become far more efficient, and this has led to lower overall costs for longer static (non-variable data) press runs.
Advances in ink technology have also improved the offset printing process. Here’s one example. UV inks, which cure instantly when exposed to UV light, have been developed and then improved in recent years. In the past, once a printer had finished printing one side of a press sheet, he had to wait for it to dry before “backing up the sheet” (printing the other side). This could take a long time. Printing the second side too soon could cause the ink on one side of the sheet to mark the other side of adjacent sheets in the stack. (This is called “offsetting.”) Offsetting could also occur when folding or trimming a previously printed press sheet. Furthermore, some ink colors dried (with exposure to heat and/or pressroom air) more slowly than others, and this could also cause unforeseen problems with offsetting. But UV ink dries instantly. That’s a major benefit.
(Sometimes printers would even flood coat the sheets to avoid needing to wait for conventional inks to dry, and this added extra costs. All of this became unnecessary with the advent of UV inks.)
In addition, one of the things that UV inks made possible was the elimination of anti-set-off powder. Prior to UV inks, a fine dusting of powder was laid down between consecutive press sheets in a stack. This powder lifted each sheet slightly above the others to minimize offsetting. This powder clogged the plates and rollers, and changed the surface texture and appearance of the press sheet. And again, it cost money.
As an added problem arising from the long waiting time for drying conventional ink (sometimes for several days), space was needed in the pressroom for the stacks of printed press sheets to dry. So all of this slowed down overall production times, wasted space, risked ink offsetting, and reduced the amount of work a printer could take into the shop at any given time. And UV inks solved the problem.
Finally, conventional inks have drawbacks such as their substrate requirements and their tendency to lose sheen and even change color during the “dryback” phase. Conventional ink requires a somewhat porous substrate. UV inks do not. Since they cure instantly upon exposure to UV light, they can be printed on non-porous surfaces such as plastic. UV inks sit up on the surface of the substrate, less ink is required, and it’s possible to maintain the bright colors (the way the ink looks right after printing) throughout the life of the product (i.e., no loss of color and sheen due to dryback). This also saves the printer money, since dryback is not always immediately apparent, and customers may reject the job or require a reprint later as the images fade or change color.
However, the first iteration of UV inks required special UV lamps that ran hot and had short lives. So energy (i.e., money) went into cooling the commercial printing plant with AC units, and still more money went into replacement UV lamps. The process was inefficient. At the same time, even the ink was expensive (compared to conventional ink). So custom printing with UV ink was not always popular.
Advances in Inks
And then things changed. UV-LED inks were developed. UV-LED curing lamps run a lot cooler than conventional UV curing lamps. Therefore, not only was the extra expense of anti-set-off powder eliminated, but the extra cost of special AC units was no longer necessary. The UV printing process became far more environmentally friendly (no VOCs, or volatile organic compounds) as well as less expensive (“typically up to 40% lower for LED,” as noted in “The Future of Sheetfed Offset”). Also, UV-LED lamps last longer.
Under these circumstances, the price for consumables was not as much of a deterrent. More specifically, as Jamie Neill notes in “The Future of Sheetfed Offset,” even if UV ink is slightly more expensive than conventional ink, you have to keep the following in mind. Paper is “typically 50-70% of the total job cost, machine time is 15-20%, etc. (but) … the typical ink cost is usually only 3% of the total job cost, on average” (“The Future of Sheetfed Offset”).
When you factor all of this in with the minimized chance that customers will reject the jobs or require reprints, the cost of UV ink becomes less of a determining factor.
The Takeaway
So advances in UV ink technology and press automation have improved the speed of offset commercial printing, reduced drying time, reduced space needed for storage of work in progress, minimized waste, eliminated volatile organic compounds, and expanded the number and kind of substrates on which commercial printing suppliers can print.
But most importantly, the color richness and fidelity (and options, if you include PMS colors as well as 4-color process inks) are still superior to digital printing. Not by much, but still superior. So for longer runs of print jobs that do not require variable data information, offset commercial printing is still a viable and valuable option.
This entry was posted
on Sunday, May 15th, 2022 at 5:30 pm and is filed under Offset Printing.
You can follow any responses to this entry through the RSS 2.0 feed.
Both comments and pings are currently closed.