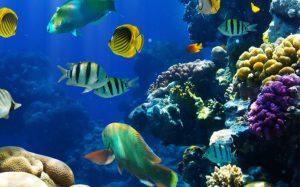
Photo purchased from … www.depositphotos.com
A striking photo can transport you into another world, just like the ocean scene pictured above.
As with most other aspects of life, in commercial printing, ensuring optimal quality for photographs while maintaining the readability of type is a balancing act.
Optimizing Photos
Photos reflect the highest contrast between tones and the greatest detail, not to mention the most faithful color reproduction, when printed on a gloss coated commercial printing sheet. There are other benefits as well. You can use more ink (because the ink sits up on top of the paper coating), and this will make the colors more vibrant. You can also use finer halftone screens (with smaller halftone dots), so image resolution will be higher than usual.
A coated bright-white press sheet reflects the most light and the purest light (unaltered by the color or tint of the paper).
In contrast, a matte or dull coating on a press sheet scatters the light. If you were to look at a gloss coated paper (with a coating composed of clay and other materials) under a microscope, you would see a flat, smooth surface. However, if you looked at a matte or dull sheet under the same microscope, you would see a rougher surface (hills and valleys). This rougher surface scatters the light reflected back to the viewer’s eyes and therefore makes the photo look less bright and crisp, with less contrast.
Printing on an uncoated press sheet carries this even further. There’s no gloss or dull coating to reflect light back to the viewer, so the overall effect is more subdued. In many cases this will even make the 4-color images (or black-and-white images) seem to have fewer gradations between tones. Also, uncoated paper absorbs commercial printing ink far more than coated paper (dull, matte, and gloss). Halftone dots of photos sit up on the surface of coated paper (called “holdout”) and retain their crispness. Colors are clean and don’t appear muddy. Details in the highlights and the shadows are visible. However, it’s much harder to maintain these qualities on uncoated paper. Not impossible, just harder.
Making Type More Readable
To complicate matters the conditions optimal for photo clarity (a blue-white, gloss-coated paper, or a gloss varnish over the images) are the exact opposite of the conditions that facilitate reading large amounts of text.
Ideally, one reads large amounts of text on an uncoated sheet (no clay coating to even out the hills and valleys of the paper surface). A light gray tint or a light yellow or cream tone (as opposed to the blue-white shade) lessens eye strain and facilitates readability as well. According to scientific studies, this actually improves reading comprehension as well (up to an 80 percent improvement, according to A Guide to Graphic Print Production by Kaj Johansson, Peter Lundberg, and Robert Ryberg). Even a matte coating or a dull coating (if you’ve selected a coated stock) is easier on the eyes than a gloss coating. Anything that diffuses the light reflected back to the viewer makes reading more pleasurable and doesn’t tire the eyes.
Therein lies the problem. You can’t have optimal conditions simultaneously for both image viewing and reading lots of text.
What’s the Solution?
Here are some options for a compromise.
First consider a matte or dull coated sheet. Either of these (dull is slightly smoother than matte and has a more even surface coating) will foster readability and will support high, if not optimal, quality reproduction of photographs.
The next option is to be creative with varnishes. More specifically, if you choose a matte or dull press sheet for a publication with both images and a lot of text, and then you gloss varnish the photos, you will get the best of both worlds. The gloss coating of the varnish on the images will make them seem crisp, detailed, and vibrant, while the dull or matte coating on the balance of the press sheet will be kind to the reader’s eyes.
Granted, this will raise the cost of printing, since you will need to use an additional press unit for the varnish. But for a high-quality publication like a coffee-table print book, this might be a good compromise.
Another option would be to print all photos (such as the color plates for an art book, which may have stringent requirements for color-image reproduction) on one press signature (on gloss stock) and place this between text-only press signatures printed on uncoated or dull-coated paper. All images would be printed exclusively on the gloss stock, while all text would be printed on the more reader-friendly paper. This was done more often in past decades, but it’s a perfectly acceptable solution now as well.
Printing on Uncoated Paper
Personally, I like photos printed on uncoated paper, even though they may not be as crisp. That said, it requires more skill on the part of the pressman to do this, and it’s harder to proof the job.
Here’s why.
The dots in a halftone (whether it’s a black-and-white image or a 4-color image) sit up on top of a coated press sheet (as noted above) but seep into the paper fibers of an uncoated sheet. All of the ink actually does this, but in an image this absorption can reduce detail in shadows or make the color seem muddy. This is due to halftone dot gain. The halftone dots expand a bit as the paper absorbs the commercial printing ink. Depending on the hardness of the paper surface, this can be more or less of a problem. If not compensated for, such dot gain can make a photo seem dull and lifeless.
However, it is possible to reduce the halftone dot size slightly in prepress, before platemaking. Back when I was an art director we called this “opening up the separations.” That is, we would ask for the density of ink in the images to be reduced by making the halftone dots slightly smaller. Then as the ink was printed on the uncoated press sheet, the halftone dots would spread (as expected on the uncoated sheet), and the overall effect would be a 4-color or black-and-white image produced with the correct amount of ink rather than too much ink.
Interestingly enough, my personal experience with this technique occurred back in the 1990s, when the commercial printing vendor would produce negatives first, and then proofs from these negatives, and finally printing plates from the negatives. Since the negatives (four process-color separations) had been “opened up,” or produced with the halftone dots having been reduced in size, the proofs were very light.
This was actually the way they should have been. If the proofs had been darker, then the resulting custom printing plates combined with the expected halftone dot gain would have produced overinked images. Nevertheless, it was still difficult to visually gauge the accuracy of the proofs because they looked very light.
Fortunately, we no longer use Matchprints and Cromalins, the proofs made from the interim negatives. Now printers burn printing plates directly from the digital information in the page layout and image editing files. Presumably these printers can digitally alter the inkjet proofs so they reflect the correct density of images on the final printed piece (i.e., the images altered to compensate for dot gain).
If this process is performed correctly by a skilled printer (both the prepress operator and the pressman), the effects can be quite nice. There’s a certain softness to the photos, but there’s also a wide range of detail in the highlights, middle tones, and shadows. At the same time, the uncoated paper supports an effortless reading experience for publications with large amounts of text.
Unfortunately, printing on uncoated paper requires a lower (coarser) halftone screen. This reduces resolution and detail. A way around this is to ask your printer about stochastic screening. Unlike traditional AM screening (amplitude modulated screening, in which a grid comprising a certain number of halftone dots per square inch stays the same while the dots themselves are made larger or smaller as needed), stochastic screening or FM (frequency modulated) screening works by keeping the dots all the same minuscule size while printing more of them in one location or another as needed to make a color darker or lighter. (This is what you see through a loupe when you look at an inkjet-printed sample.) This also provides a much higher perceived image resolution than can be achieved with traditional AM screening.
Paper Color Makes a Difference
I noted above that a yellowish-white (or cream) tone can make reading easier. While this improves the readability of text, it can cause problems with photos. This is because process inks are transparent. Therefore, the color of the substrate affects the colors printed on the paper. So if you’re printing groups of people, or portraits, on a cream stock, the yellowish tinge can make the flesh tones seem a bit yellow. You should be mindful of this when selecting a paper stock for your publication (and perhaps even request printed samples from your commercial printing vendor).
This entry was posted
on Sunday, March 20th, 2022 at 3:06 pm and is filed under Paper Coatings.
You can follow any responses to this entry through the RSS 2.0 feed.
Both comments and pings are currently closed.