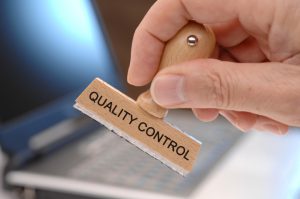
Photo purchased from … www.depositphotos.com
Accuracy/quality/precision–in the little things–is important. This includes precise grammar. It also includes clean, precise printing and finishing work in a publication, a brochure, or even a sign. If something looks wrong in a publication, within the design or within the print production itself, it is only natural for the reader to question (even subconsciously) the accuracy of the content. And this can make you lose your reader’s interest.
In this light, I have selected six printing errors that you may want to look for if you are doing a press check (if your job needs to be of showcase quality) and that your printer always looks for because he wants your commercial printing work to shine.
These six errors are scumming, doubling, slurring, hickies, setoff, and web pull. These are just a random handful for one article. I have addressed other issues, such as ghosting and density problems, in prior articles. All of these are referenced in Getting It Printed by Mark Beach and Eric Kenly. You may want to do further research into custom printing problems online or ask your print provider for suggested print books on the subject.
At the very least, your appreciation for your printer’s knowledge and eyesight will grow as you learn more about potential commercial printing flaws. For now, here are six of them.
Scumming
Offset lithography works on the concept that oil and water don’t mix. An offset printing plate can have the image area and non-image area on the same flat surface (unlike the recessed image areas of intaglio printing or the raised image areas of relief printing) because of the immiscibility of oil and water.
For oil-based custom printing inks to adhere to image areas of the printing plate (for transfer to the press blanket and from there to the paper) and not to non-image areas, the ink/water balance must be correct. Printers learn how to do this. If the balance is not maintained (or, more specifically in this case, if there is not enough water), ink will print in non-image areas. For instance, tails of ink may appear to streak outward from the letterforms of type. Or streaks of ink may run down the press sheet. This is called scumming. Watch for it (check the samples your printer pulls every so often during the press run as a quality check, if you attend a press inspection). Your printer will be checking this ink/water balance throughout the commercial printing process.
Doubling and Slurring
As the press rolls, the plate transfers the image to the rubber press blanket, and then the blanket transfers the image to the paper substrate (hence the term “offset,” because the plate does not print directly on the paper). If the blanket hits the paper a second time (perhaps a light touch), the halftone dots will appear to blur. This is called dot doubling.
If there is a problem with inaccurate press blanket pressure or poor ink tack (the stickiness of the ink that allows it to pull off the plate onto the blanket and off the blanket onto the paper substrate), halftone dots can become elongated. This is called slurring.
The difference between doubling and slurring is that in doubling, there are duplicate halftone dots and each halftone dot has its own slight shadow. However, in slurring, there are the proper number of halftone dots, but the dots are oblong (i.e., stretched), not round.
When you are doing an on-site press inspection at the printer’s plant, you may not see these flaws directly on the press sheet. However, they may be visible on the printer’s control targets (GATF color control bar, for instance) for dot gain, slurring, and doubling. Also look for dot gain targets and color patches for solids, screens, and overprints. Printer’s quality control bars are on the outer perimeter of the press sheet, outside the live image area of the print job.
You can find a detailed description of these printers’ control targets in Getting It Printed (Mark Beach and Eric Kenly).
Hickies vs. Picking
If your commercial printing plates and blankets have not been adequately cleaned, bits of dust and paper fibers will attach themselves to these surfaces and prevent adequate application of ink. You can identify these marks on a printed press sheet as tiny white donuts with solid ink centers. These can be minimized but not eliminated entirely by proper cleaning of the blankets and plates. Over the course of the press run they will appear on a few or several press sheets and then will just as quickly disappear. These are called hickies, and they are the result of ink particles, paper or coating flecks, press dirt, and dust getting where they shouldn’t be. Hickies are most obvious in large flat areas of color.
In contrast, ink picking refers to the ink’s tack (or stickiness) pulling off particles of the paper surface or paper coating. Good quality printing paper will resist this flaw.
Set-off
Once a printer has finished printing a stack of press sheets, if he wants to turn over the pile and print the other side of the press sheets, he must first wait for the ink to dry. Otherwise, the ink will set off from one press sheet to the back of the adjacent press sheets during the printing of the second side (printing the opposite side is known as “backing up the sheet”). However, even if the printer does not try to back up the sheet when the ink is wet, the image can still offset due to the weight of the press sheets on one another.
To avoid this, printers spray anti-set-off powder on the wet press sheets. The fine particles of the anti-set-off powder slightly lift one sheet above the next and protect the ink while it dries.
Processing press sheets in any way (not only printing the second side but also folding and trimming the press sheets) prior to the ink’s being dry can be problematic and can also cause offsetting. Therefore, don’t push your printer. Let him take the time he needs for the ink to dry. Keep in mind also that certain colors of ink take longer than others to dry, and large, heavy-coverage ink solids require more drying time than areas of light ink coverage.
Web Pull vs. Web Growth
When the roll of web paper goes through a heatset web press and receives ink, the paper ripples slightly due to the heat and moisture. Then the heat of the web press ovens bakes these ripples into the paper so they are permanent. Some printing paper reflects this flaw more than other printing paper.
This gets even more problematic when a web-fed press prints the text of a print book and a sheetfed press prints the covers. The heat of the heatset web press ovens evaporates the water in the text paper fibers prior to the printer’s attaching the paper covers. Over time (and after the trimming process), the paper in these text blocks absorbs water and grows.
However, the covers, having been printed via sheetfed offset lithography, are not exposed to the high heat of the ovens of the web-fed presses that printed the text blocks of the books. Therefore, the text paper grows, but the cover paper does not.
If both cover and text paper were printed on the same kind of press, this would not be a problem, but since the covers are applied to the text blocks and then the books are trimmed, as time progresses the interior of the print books will absorb moisture and can grow beyond the trim of the covers, making a thin strip of the interior text of the books visible beyond the trim of the book covers.
Like the web pull noted above (the rippling of text paper baked into the wet press sheets), web growth cannot be completely eliminated.
The Takeaway
-
- Understand what kinds of flaws your printer is seeking to avoid, and appreciate his level of knowledge and attentiveness.
-
- Attend a press inspection now and then to really understand these potential flaws.
-
- Read books or online articles on these subjects, and ask your printer about the potential flaws when you attend a press inspection.
- It actually benefits both you and your printer for you to understand which flaws can be avoided and which can only be minimized due to the nature of offset commercial printing.
This entry was posted
on Saturday, February 26th, 2022 at 8:51 pm and is filed under Printing.
You can follow any responses to this entry through the RSS 2.0 feed.
Both comments and pings are currently closed.