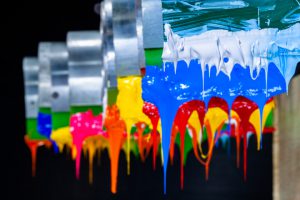
Photo purchased from … www.depositphotos.com
My First Screen Printing Experience
The summer before college I worked (one on one) with a Mexican ceramics artist. He was the artist in residence at a church attached to a local high school. Night after night I would take a bus to his studio and learn (of all things, not pottery making but) custom screen printing. He was skilled at both disciplines.
I learned a lot over these months. I brought in a hand-drawn surrealistic image in multiple colors. The first thing I learned was just how labor intensive the process of screen printing was. For each color I had to cut a separate mask (or stencil), removing selected bits of a plastic block-out sheet I had attached to the nylon screen with adhesive. I cut with a small, sharp knife point and then peeled away any masking plastic in areas that would print.
Each time I would finish preparing the mask (on the screen) for a particular color of the 6- or 8-color job, I would attach the framed screen (silk stretched over a wood frame) to the hinges on the base board, pour thick, brilliantly colored screen printing ink onto the far side of the screen-printing frame, and lay a sheet of paper between the screen and the base. Then, using a squeegee (a rubber strip on a wooden handle the width of the wood frame), I would draw the ink across the screen.
The ink would seep through (literally, because it was such a thick ink) the screen and onto the paper. Anywhere I had removed the plastic masking material attached to the silkscreen, the ink would flow through the screen and onto the paper. Anywhere I had left the plastic sheet intact, this block-out stencil would keep the ink from reaching the paper.
So I would print sheet after sheet this way, starting with the first color. Then I would remove the plastic block-out sheet from the screen completely, wash everything down, prepare the next stencil for the next color, and print each and every sheet on which I had printed the prior color.
It was a long, long process, from the inception of my design to the finished stack of screen prints. Night after night I would do this in the ceramic artist’s studio. I appreciated how thick the ink was, and how intense its color was. It was a good education. I never forgot the patience it required.
Using Screen Printing at the Art Museum
Within the same time period before college (during the day), I also had an internship at a DC modern art museum. Since I was getting an education in custom screen printing at night, I was particularly alert to how the art museum used screen printing to prepare for an upcoming exhibit. They would screen print the three- or four-paragraph description of each painting (and explanations related to each room in the exhibit) right on the wall. This intrigued me.
So I asked some questions and did some research, and I learned that they had prepared the screens with a photographic emulsion. Using typeset material as a starting point (either projected onto the silk screen or attached to a clear acetate sheet), they projected ultraviolet light through the mask or stencil. Where the light reached and exposed the photo-sensitive emulsion (UV light-sensitive rather than visible-light sensitive) on the screen printing fabric, this light hardened the emulsion.
Everywhere else, the emulsion had not hardened. As the screen was washed (the next step), the water removed the emulsion that had not been exposed to UV light, leaving the typeset words as “holes” within an otherwise opaque mask over the screen. Museum staff could then hold the screen (loaded with ink) up against the wall, draw a squeegee across the frame, and transfer the screen printing ink through the mesh and onto the wall. Once the screen had been removed, there it was: the typeset paragraphs explaining the exhibit or the specific art piece.
In this particular case (unlike the silkscreen I was producing at night in the artist’s studio in the church), these wall screen prints were one color. So registering one color to the next (as I was doing at night) was not an issue.
Moreover, in my case, I was cutting the masking material with a knife (shapes of color, not intricate typescript), and at the museum, the process of preparing the screen was a chemical and photographic (rather than manual) one. I learned later that the same process they were using could be used for photographic halftones and even multiple-color halftones (just using a coarser halftone screen ruling than for offset lithography).
So printing was in my blood by the time I was 18. Both of these experiences (learning silkscreen with a Mexican sculptor/potter and working at an art museum) paved the way for the following forty-five years’ work in all aspects of fine art, commercial art, publications management, and commercial printing.
What Else Can You Use Screen Printing For?
Having had these formative experiences, I was aware of and highly alert to custom screen printing, also called serigraphy, in my work. I noticed that screen printing was great for objects that couldn’t be offset printed. (For example, you can’t run a 3-ring binder through an offset press, but you can use a screen, or multiple screens, to print on the vinyl-covered boards of such a binder.)
You can also print on hats, mugs, messenger bags. If you Google “promotional items,” you will see all number of functional products you can embellish with custom screen printing. In fact, if you look closely at these printed products, you will see just how thick the ink is. It’s like paint. And I for one believe that this thick ink projects an air of opulence.
Wallpaper is another product that lends itself to custom screen printing, particularly since there are cylindrical screens (the screen I was using at night and the one used at the museum were flatbed screens) that allow for essentially continuous custom printing of patterns. In this case, the ink and squeegee are inside the rotary screen, and the cylindrical press can be rotated again and again to create and endless pattern.
T-shirts as well as other similar garments are also often screen printed. In fact the ink can be formulated to puff up slightly above the garment’s surface, to be metallic, or to have the texture of suede.
Signs are another lucrative custom screen printing market. And in most of these industrial printing venues the screens are not silk, as mine was, but either stainless steel, nylon, or polyester mesh. The finer the mesh, the finer the halftones. However, fine screens can easily plug up, since the ink is especially thick, so this does limit the fineness of the line screen used for halftone images.
And finally, the substrates don’t have to be paper or fabric. You can print on metal, plastic, wood, ceramic, even glass.
Screen Printing vs. Digital Printing
In all of these cases, the products have been made on custom screen printing presses, either single-color frames or in some cases (for multi-color t-shirts, for instance) a carousel of screens attached at a central point. These screens can be rotated into and out of the image-printing area to speed up the process.
But it is a time-consuming process nevertheless, with all the screen preparation, printing, and cleaning steps.
Back when I was screen printing the surrealistic design at night, and watching the museum staff screen print text on the wall during the workday, it was the late 1970s, so digital printing had not yet been invented.
Now, many of the products manufactured with custom screen-printing technology can be produced with inkjet printing technology in some cases and dye sublimation technology in others (such as printing on mugs). This now allows for variable-data printing. In fact you can make each item different, which you can’t do with screen printing.
That said, there’s still room for screen printing in product design (i.e., functional printing or industrial printing). For instance, you might want to print special conductive inks on printed circuit boards that will be used for electronic devices. Or you may want to screen print text on the control panels of microwave ovens.
Screen printing is still out there, still an ideal technology for specialized uses. However, it’s best suited to longer runs, due to the labor-intensive processes it involves.
This entry was posted
on Friday, November 12th, 2021 at 7:07 pm and is filed under Screen Printing.
You can follow any responses to this entry through the RSS 2.0 feed.
Both comments and pings are currently closed.