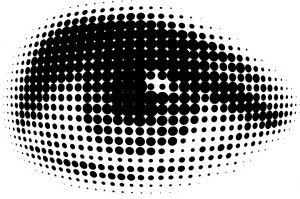
Photo purchased from … www.depositphotos.com
Offset printing, which has been around for a long, long time (since the mid 1870s), is based on the proposition that oil and water do not mix, and that if you draw on a custom printing plate with a greasy substance like ink, and then flood the non-image area with water (in a precise ink/water balance), ink will adhere to the image area and be repelled by the water in the non-image area. The ink can then be printed on a press blanket and from the blanket to a paper (or other) substrate.
This is a chemical process. It is also rather time consuming (to keep the ink/water balance correct), and it uses a lot of water and paper in the process. Moreover, since offset lithography is an art as well as a science, there’s considerable skill required to achieve a successful ink/water mix.
Heidelberg Quickmaster DI (Waterless Offset)
With this in mind, consider a process I learned about in the early 2000s from a printer who had a Heidelberg Quickmaster DI on his pressroom floor. This press imaged plates right on the press (no negatives, which had been the norm a few years prior, and no platesetter, which was the current technology). It used silicone-covered plates.
A laser burned the image areas of the plate, removing the silicone, and the silicone on the rest of the printing plate repelled the ink while the image areas with no silicone attracted the ink. In fact, the process was no longer exactly planographic (image area and non-image area on the same flat surface). There were slight indentations where the silicone had been removed. So the process was actually closer to “intaglio” (a recessed image area on a plate, just like an engraving plate or a gravure cylinder). It was also more of a physical process than a chemical process (unlike conventional offset lithography). And it allowed for a thicker ink film, since the commercial printing ink collected in the recessed areas of the plate where the silicone had been removed.
That said, the process did not use water, or alcohol, since there was no need for a dampening fountain solution. So it was possible to print halftones with much higher line screens than usual (300- to 800-line halftone screens rather than the usual 175-line screens). Stated more precisely, the images were spectacular.
Now all of this occurred on a DI (direct imaging) Heidelberg press, used at the time for short runs of static printing (unlike the variable data printing of an inkjet press or laser printer).
Just out of curiosity I recently did some research to see if the technology was still in use (also because the last time I had written about waterless offset for the Printing Industry Exchange was in 2007).
The State of the Art
I found an article in Africa Print (07/08/2019) entitled “The Benefits of Waterless Offset Printing,” and I was pleased to see that the process was still in use: not necessarily on the Heidelberg Quickmaster, but on retrofitted offset presses in general. And I learned that the process offered serious benefits to the environment.
This is what I read in “The Benefits of Waterless Offset Printing”:
-
- A B1 (28” x 40”) press running two shifts will consume up to 200 liters of water a day (52.833 gallons) and 1,000 to 1,200 liters of alcohol a month (alcohol is a component of the fountain solution used to keep ink and water separate on the custom printing plates). This is 264.172 to 317.007 gallons of alcohol.
-
- Making IPA alcohol for commercial printing presses and transporting multiple thousands of gallons to printers each year costs a lot, consumes energy, and contributes negatively to carbon emissions.
-
- Also, contaminated water has to be treated as hazardous chemical waste.
-
- As I had noted earlier, traditional offset lithography consumes extra paper, ink, and fountain solution as waste (i.e., producing unusable printed copies) in achieving the correct ink/water balance and in getting the press “up to color.”
- Since fresh water is becoming increasingly scarce (especially in other parts of the world, such as Africa, where this article was presumably written), the use of copious amounts of water by offset commercial printing is a problem.
Enter Waterless Offset
What’s nice about waterless offset, also known (in my research) as “driography” (3M’s version of the process used in the late 1960s), is that you don’t need to buy a new press. You can retrofit your existing commercial printing press to use waterless plates and the waterless offset custom printing process.
Waterless offset seems to be the same as the process I learned about in the early 2000s as used in the Heidelberg Quickmaster DI press (silicone-covered plates with image areas burned off with a laser).
Here are the benefits as noted in “The Benefits of Waterless Offset Printing”:
-
- Waterless offset can be done on conventional presses.
-
- No water is used in the custom printing process.
-
- Since the balancing of ink and water is no longer an issue, it is possible to get the press “up to color” much faster, significantly reducing the paper waste usually attributable to makeready.
-
- Faster makereadies mean printers can complete jobs faster and therefore economically produce shorter press runs than heretofore.
-
- Not using water means it is possible to print on non-absorbent substrates, including plastics and metal.
-
- This also includes printing on currency, identification cards, passports, and such, using security inks.
-
- Due to the lack of water in waterless printing, it is possible to use finer halftone screens (upwards of 300 lpi to 800 lpi), and this makes printed images look almost like continuous tone photos. According to “The Benefits of Waterless Offset Printing,” it’s even possible to convert newspaper presses to be used for much higher quality commercial printing work.
-
- Given the relatively inexpensive transition of presses to waterless offset, as well as the relatively minimal training needed, this is an attractive proposition for most commercial printing suppliers. Even if the plates and other materials are a little more expensive than those used in traditional offset, the savings in the makeready stage still makes this financially feasible.
-
- And an additional article I found, “Toray Develops First Waterless Offset Printing Press,” 09/17/20, by Toray.com, notes that water soluble UV inks can be used, obviating the need for solvent based inks and the equipment and energy used for drying solvents and processing the resultant exhaust gases.
- Plus, wash-ups of press equipment can be done with water-based products instead of solvents (“Toray Develops First Waterless Offset Printing Press”).
So the answer to my initial question seems to be a resounding yes. The waterless offset process is still very much in use.
Where to Go From Here
If this interests you, as a designer, printer, or print buyer, start researching the topic online. Once you understand it, you can start your search for vendors who offer this process. It seems from my research that such vendors won’t be hard to find. The planet will appreciate your efforts.
This entry was posted
on Monday, May 10th, 2021 at 11:03 am and is filed under WaterlessPrinting.
You can follow any responses to this entry through the RSS 2.0 feed.
Both comments and pings are currently closed.