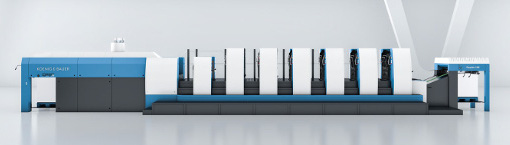
from https://www.koenig-bauer.com/en/products/sheetfed/sheetfed-offset/medium-format/rapida-106/
I’m always pleased when I see, in an increasingly digital world, that offset commercial printing is still relevant. Interestingly enough, this is because OEMs (original equipment manufacturers) are paying attention to their customers’ needs for speed, economy, and quality.
I read a Koenig & Bauer press release this week about the new Rapida 106 X. This is a “high-performance sheetfed offset pres for the medium format 740 x 1060 mm.” (K&B press release, “Koenig & Bauer Introduces the Rapida 106 X for Industrial Printing”). Translated into inches, this is a 29” x 41.73” press, large enough for efficient printing. (Longer multi-page press signatures mean fewer press runs, and larger press sheets allow for more large-format jobs, like flat pocket portfolios before their being folded and glued.)
But it’s not just the press-sheet size that makes the Rapida 106 X special. Here are the benefits that K&B notes in its press release.
Benefits of the K&B Rapida 106 X
“Shorter makeready times—faster into print” (K&B press release, “Koenig & Bauer Introduces the Rapida 106 X for Industrial Printing”). Offset lithography has to compete with digital commercial printing to earn its share of customers. One way to do this is to minimize one of the major drawbacks of offset lithography: the long makeready process. K&B has achieved this goal on the Rapida 106 X. This press can perform “simultaneous plate changes in less than a minute with unbent and process-free plates” (K&B press release, “Koenig & Bauer Introduces the Rapida 106 X for Industrial Printing”). This means that the Rapida can perform parallel, autonomous makeready processes, not only within a job but between jobs, doing the plate changes without operator intervention. All the pressman has to do is monitor the process via the digital interface. If he tried to make these plate changes by hand, it would actually take much longer.
What This Means
The K&B press release uses a 350-sheet job to illustrate the point. Normally, a job this short would go on a digital press (toner-based or inkjet). But what if you need the slightly higher quality of offset lithography? Or maybe you need precise PMS colors instead of 4CP process match colors. You could still do the job efficiently on the Rapida 106 X, even factoring in multiple plate changes (removing the old plates and loading the new ones automatically during the press run).
“Higher speed—even faster in production” (K&B press release, “Koenig & Bauer Introduces the Rapida 106 X for Industrial Printing”). One of the main benefits of offset lithography is that it’s fast. Once you put the time in up front to set up the process, the 18,000 to 20,000 sheets-per-hour commercial printing speed will outpace even the fastest of the larger-format digital laser or inkjet presses. In this case, the Rapida 106 X will not only print up to 20,000 29” x 41.73” sheets per hour, but it will do this in perfecting mode (printing both sides of the press sheet simultaneously, which usually slows down overall throughput).
What This Means
When you’re perfecting a print job, you don’t have to bring the pile of finished press sheets (printed on one side) around to the front of the press (once the ink has had time to dry) and send all of the sheets back through the press to print the other side of all press sheets (called “backing up” the sheets).
In addition, the digital interface (such as K&B’s Job Optimizer) links all processes (prepress and press functions) based on “technological or press-related considerations” (K&B press release, “Koenig & Bauer Introduces the Rapida 106 X for Industrial Printing”). The press electronically chooses the best workflow (order of jobs based on press form size, sheet size and format, paper weight and surface coating, etc.). According to K&B, this can shorten make-ready times by an additional 30 to 50 percent. Moreover, by closely and instantly tracking all operations, managers can precisely measure the exact cost of all processes.
“Reliable processes—stable in production” (K&B press release, “Koenig & Bauer Introduces the Rapida 106 X for Industrial Printing”). Quality is everything. Speed by itself isn’t good enough. Using cameras (either one for straight-line printing or two for perfecting) on press, the K&B Rapida 106 X can accurately control color, instantaneously and continuously monitor the press sheets, and compare the press sheets with prepress PDF files (via QualiTronic PDFCheck or QualiTronic PDF HighRes). The Rapida 106 X uses QualiTronic ColorControl to read ink densities on every sheet (as opposed to every 10 sheets, or whatever other number had been chosen, as was the case when I was doing press inspections in the 1990s). The software can check the color bars on each sheet and make adjustments every ten sheets. When getting the press “up to color” (i.e., getting the color densities exactly right), the press scans and registers the good sheets and then compares all subsequent sheets to this target. It can scan the sheets at either 100dpi or 290dpi (using additional cameras), so any variance between the press-ready PDFs and the press output can be corrected immediately.
What This Means
When the flaws show up immediately, and the corrections are made automatically, the whole process goes much faster. The K&B Rapida 106 X comes up to color much faster than prior presses, and the number of waste sheets used in the process drops to between 25 and 50 sheets. (And on a completely different note, this process monitoring can be done remotely on a mobile device using the Rapida LiveApps ErgoTronicApp.)
“Less maintenance—more time in production” (K&B press release, “Koenig & Bauer Introduces the Rapida 106 X for Industrial Printing”). Since all performance data is logged in real time, the Rapida 106 X makes maintenance and repair much easier. More specifically, before a repair is scheduled, the log can be accessed remotely (along with photos, videos, and audio files), and many problems can be resolved from a distance.
What This Means
All of this means less downtime. When the press is running, the printer makes more money, and the clients get their jobs on time. Moreover, using artificial intelligence along with camera footage from the press, operators and maintenance engineers can analyze trends and identify faults in the operation in real time, while keeping the presses running.
Why It’s Good That We Still Have Offset Custom Printing
Ultimately, time equals money. If you’re producing a short-run, simple job, you’re going to choose digital commercial printing. This will involve either laser or inkjet technology. The quality level is now extremely high, particularly when compared to what it was when I was an art director in the 1990s.
That said, if you’re producing a long-run print job, then an offset press that can print up to 20,000 sheets per hour (with, perhaps, a 16-page press signature of a book being imaged on each press sheet) is a blessing. The job flies through the press. And the more you print, the less each copy costs. It can’t be beat.
You can also print on a much greater variety of press sheets with a greater variety of press finishes.
Or maybe you want to print a metallic ink. Or maybe you have specific corporate colors that you need to match with PMS inks. Offset lithogaphy is your best choice in both cases.
Finally, as good as digital printing has gotten, in my own humble opinion, the detail and color accuracy of offset lithography just can’t be beat.
So all of the artificial intelligence, camera-monitoring, trend analysis, and automated workflow and plate management additions K&B has introduced to the Rapida 106 X have leveled the playing field, allowing you to choose either offset or digital technology for even a short press run.
This entry was posted
on Monday, July 20th, 2020 at 1:56 pm and is filed under Printing.
You can follow any responses to this entry through the RSS 2.0 feed.
Both comments and pings are currently closed.